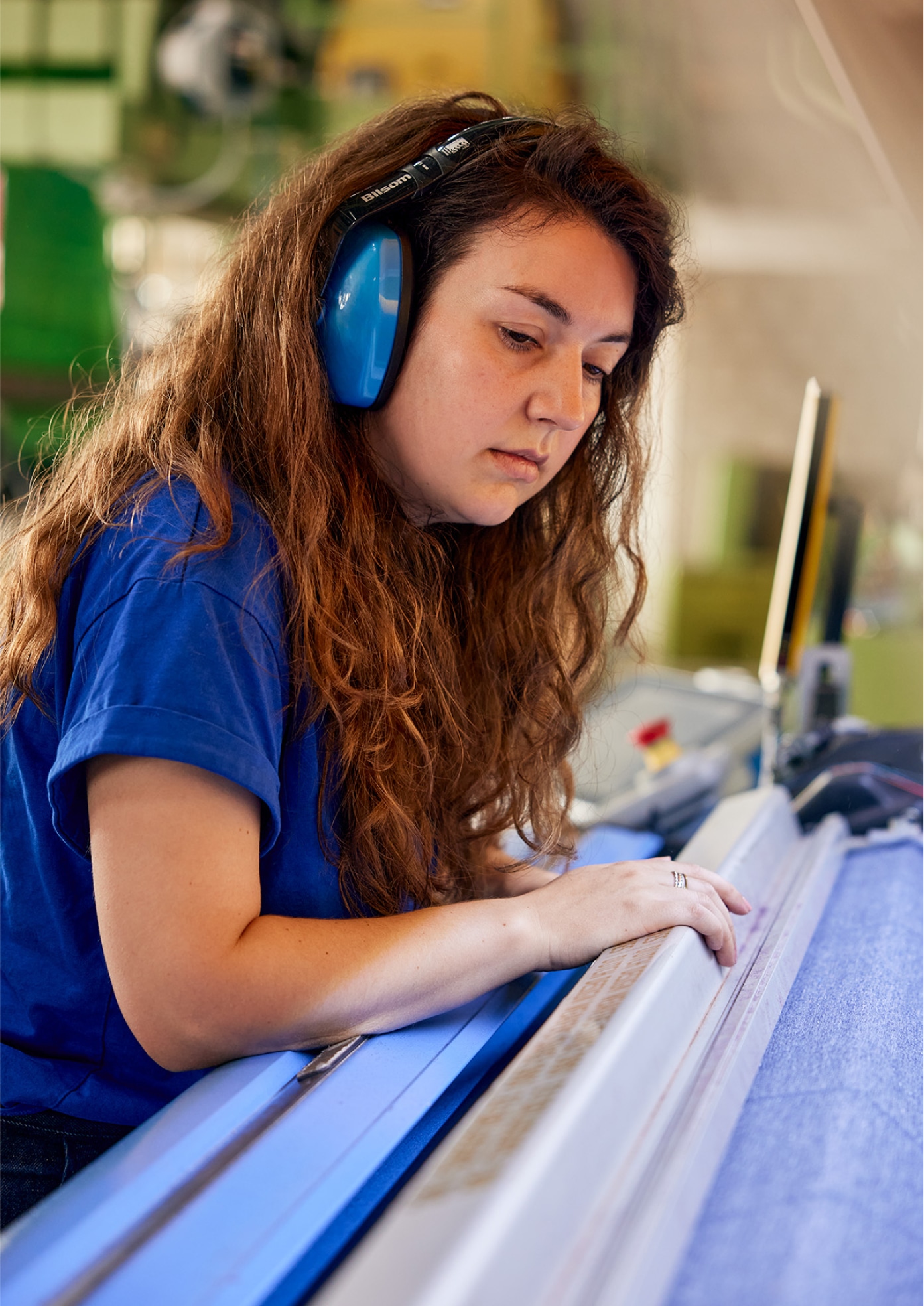
Studio Milou Voorwinden
Milou Voorwinden
Milou Voorwinden is innovating the existing fashion and textile industry by developing 3D weaving techniques. She is creating a 'fold-out' fabric, which comes right off the loom as a complete garment, such as a pair of trousers or a bag. This on-demand approach results in zero-waste.
The garment industry is one of the biggest polluters in the world, generating a significant amount of waste during production. Just processing a piece of textile into a fashion item generates 15-20% material waste. Additionally, 30% of the clothes produced end up as waste due to overprodution by clothing labels. Consumers also throw away a large proportion of the clothes purchased within a year, because the next trend beckons or the clothing doesn't fit properly.
According to Milou, this has to change. We spoke with her about her love of craft and making processes, as well as her role as a materials expert and innovator.
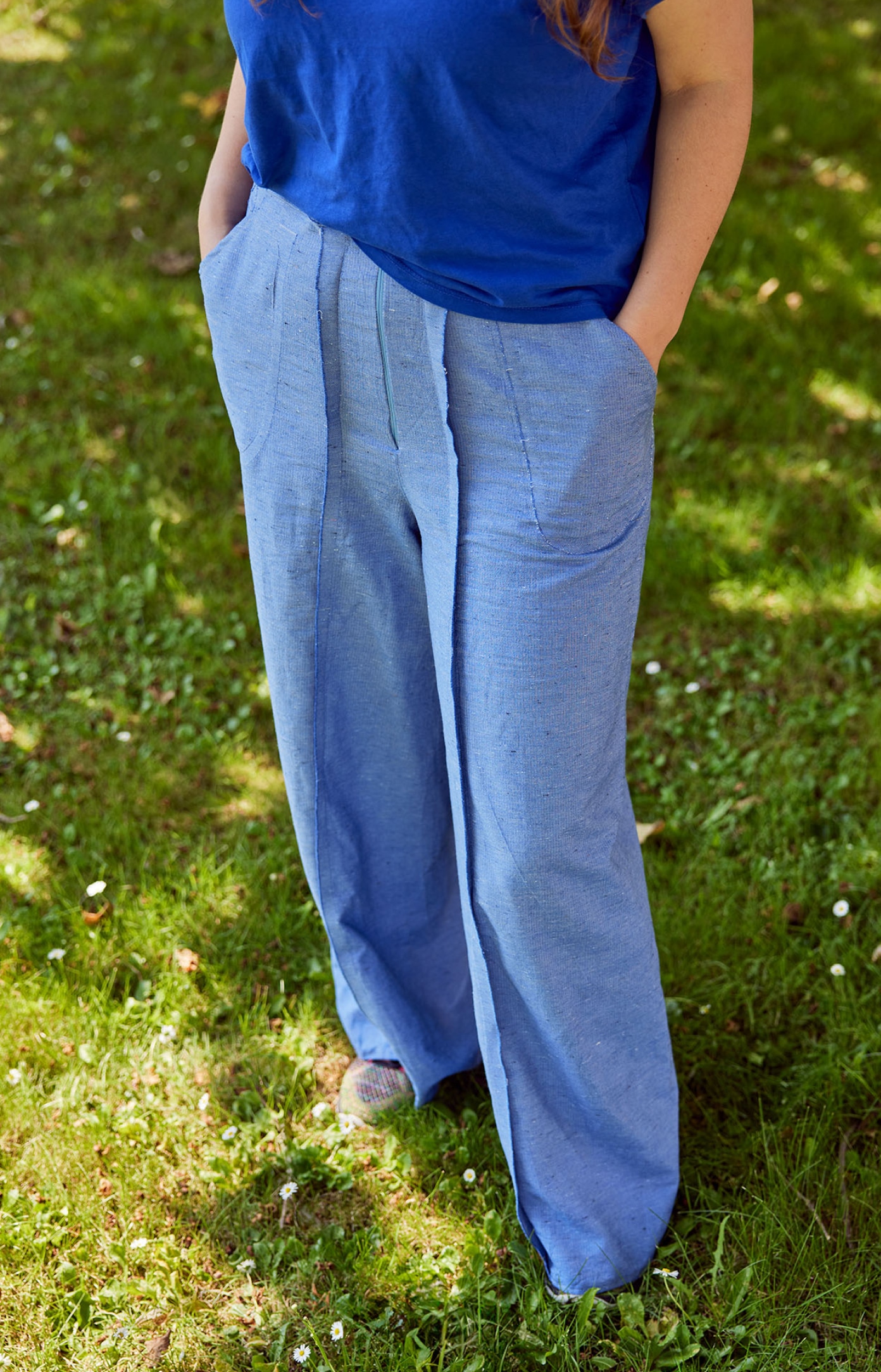
Photography: Anouk Moerman
Hi Milou, what drives you, what is your passion and where does it come from?
My love for textiles runs in our family, my grandmother knitted a lot and my mother is always crocheting or knitting too. From them, I learned that with a few simple elements, like a ball of wool and some knitting needles, you can create beautiful things.
I initially wanted to become a jewellery designer, here too you only need a few things, a thread and some beads, and you can vary endlessly with colours and patterns, but an allergy prevented me from pursuing that path. So I switched to studying product design, where I began focusing on textiles. While working on an assignment, I became interested in the structure of how fabrics are actually put together. The way you can determine the properties of textiles by manipulating the threads. This led me to ask myself if it was possible to weave an entire product in one go. This interest in making and using woven materials in an innovative way drew me deeper into the textile industry.
Can you take us into the textile industry, what do you think could be improved here?
Gladly, specifically the clothing industry. Although everyone wears clothes, and therefore textiles, few people are aware that sewing different pieces of fabric together to make a garment produces a huge amount of waste.
Let me explain. Currently, textile production for clothing is focused on weaving flat fabrics, which are cut up and sewn together into garments. The production of those fabrics is entirely focused on mass production and cost-saving measures. I saw this firsthand last year when I visited a weaving factory in Pakistan. There, dozens of large, modern looms were set up to produce rolls of fabric as quickly as possible.
In the next stage, different pattern pieces are cut from the woven fabrics based on standard clothing sizes. These are then sewn together to create garments. Per garment, this method generates 15 to 20% cutting waste, often in the form of quite large pieces of fabric, which go straight to the landfill. Of the clothes that are produced, an additional 30% end up in this landfill because clothing labels produce much more than they eventually sell. And on top of that, most of the clothing that’s purchased is thrown away by consumers within a year, either because there is a new trend, or because they don't fit properly.
Fabrics which come right off the loom as a complete garment, such as trousers or bags.
What is your solution for reducing waste in textile production?
Most textiles produced consist of a single layer of fabric. I am developing a method to weave multiple layers at the same time. This is called 3D weaving, and with it you can make fold-out fabrics, which come right off the loom as a complete garment, such as trousers, jackets or bags. This technique makes it possible to produce on-demand, creating a more sustainable alternative to traditional garment manufacturing.
Developing this 3D weaving technique requires innovation of the weaving craft, and adaptation of existing machines. I have been working intensively on this since 2017, collaborating with experts in the field, such as weaving company EE Labels and Enschede Textile City. Last year, I started a PhD at TU Delft's Faculty of Industrial Design to further investigate 3D weaving. Together with my supervisor Holly McQuillan - an expert on zero-waste design - we developed a method that allows for weaving 3D garments.
You talk about 3D woven trousers, jackets or bags. Can you explain how that works?
Yes, it works like this: to weave customised 3D woven trousers, we enter the measurements into a design application. This application then creates a digital avatar - a miniature virtual representation of a person. The avatar ensures that the design will fit properly. The design, which has a 3D shape in the application, must then be flattened so that it can be woven. The outcome of this process is a drawing with many colours: each colour indicates how the different layers of fabric are connected. The drawing is then translated into a file that the weaving machine can read.
Once the trousers are ready, all you have to do is cut a few threads, and a complete pair of trousers will unfold. You will still need to sew on a button or insert a zip, but the trouser pockets, for example, are already woven in.
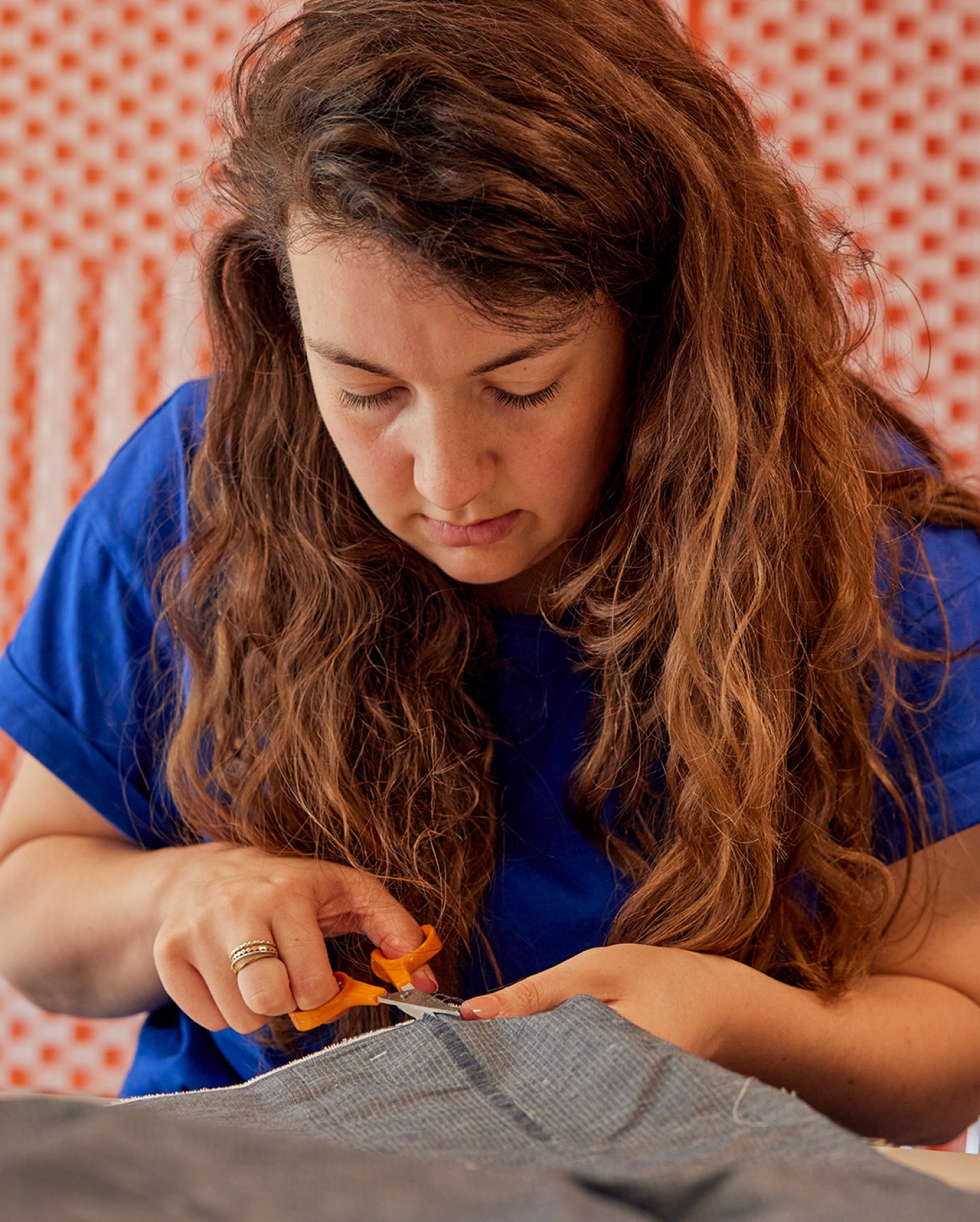
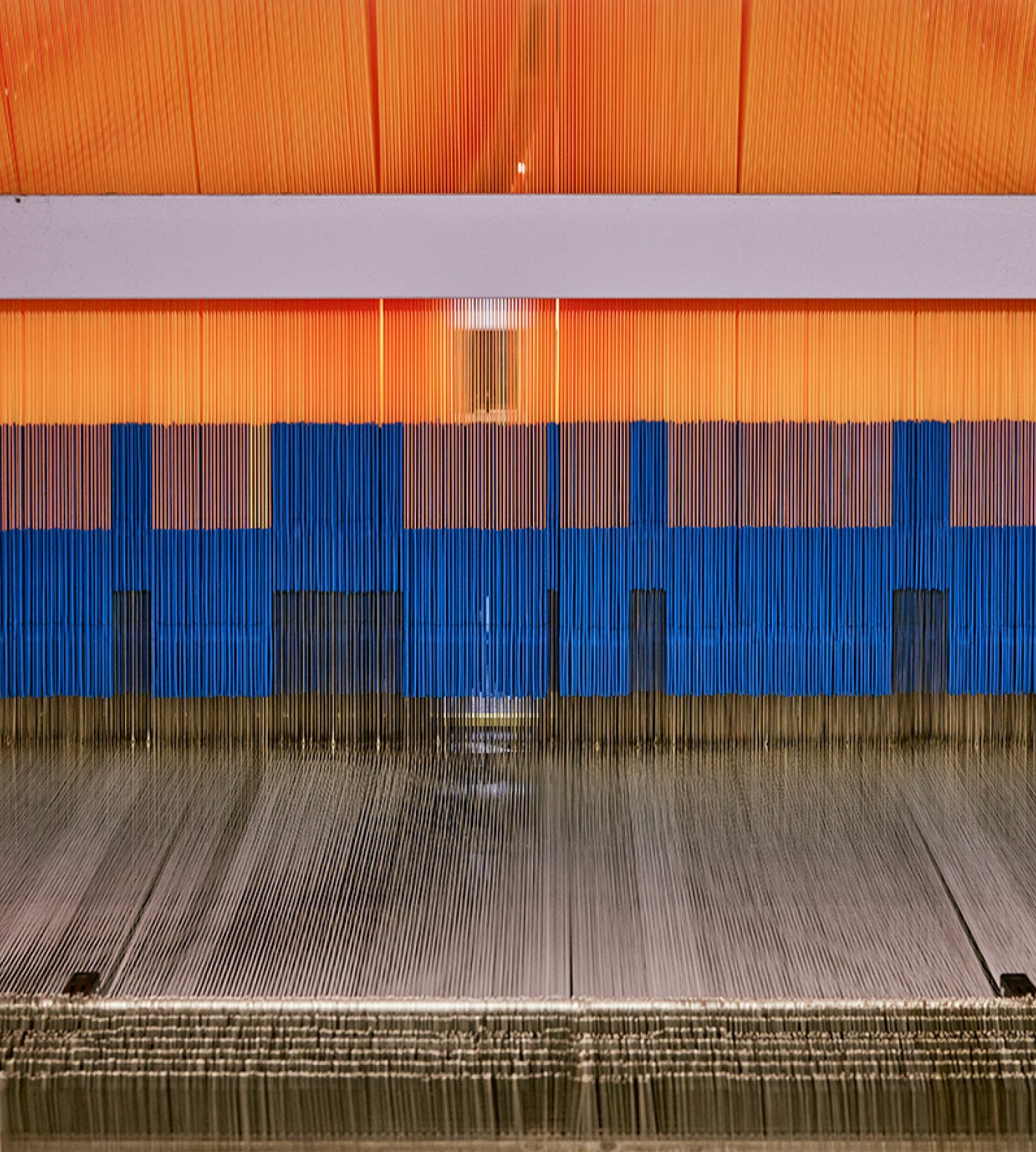
Are such garments already available in the market?
We are now at the stage where we can weave high-quality prototypes, and we have been able to develop several types of garments together with students from TU Delft. But my primary focus in this process is on developing the technology for the industry rather than marketing the garments themselves. By creating prototypes, I want to not only demonstrate what is possible, but also find out what is needed to implement these techniques in the industry.
I deliberately chose to focus on innovating the current industry and developing this new technology for existing weaving machines. This approach has a great advantage of being more accessible to the manufacturing parties, as it requres less investment compared to purchasing dedicated 3D weaving machines. However, adapting existing machines for 3D weaving is a complex process, as they are designed for producing flat textiles, not 3D ones.
So, are you managing to get the industry to start weaving 3D and waste-free with their existing machines?
The technology for producing 3D garments is now available, but transitioning the industry to this new method presents significant challenges. Generally, the cornern is that my method is too difficult or too expensive. Therefore, it is important that I have a very good command of the weaving technique myself and know their machines inside out. This way, I am not dependent on technicians telling me that something can or cannot be done, and it allows me to demonstrate that my ideas are indeed feasible, despite their complexity.
By gaining first hand experience with the weaving machines and processes, I can effectively communicate with the industry. Their attitude changes as soon as they notice that I have mastered the technology myself. There is also a curiosity within the industry as they realise we cannot continue producing in the current way.
The industry is curious, what can you offer them?
The technology for producing 3D garments is now available, but transitioning the industry to this new method presents significant challenges. Generally, the cornern is that my method is too difficult or too expensive. Therefore, it is important that I have a very good command of the weaving technique myself and know their machines inside out. This way, I am not dependent on technicians telling me that something can or cannot be done, and it allows me to demonstrate that my ideas are indeed feasible, despite their complexity.
By gaining first hand experience with the weaving machines and processes, I can effectively communicate with the industry. Their attitude changes as soon as they notice that I have mastered the technology myself. There is also a curiosity within the industry as they realise we cannot continue producing in the current way.
There is a curiosity within the industry.
You dream of great improvements, but designing 100% sustainably is difficult. What dilemmas do you run into?
I used to think that in order to develop a successful design, every decision I made had to be perfect. I have since learned that even with an imperfect design, you can inspire and change. It’s about finding the right balance and making informed trade-offs.
For example, the trousers Holly and I developed are made of a blend of polyester and cotton. While I prefer to avoid polyester, the weaving machine at EE Labels, where we created the prototype, currently uses polyester threads.
Replacing these threads with another material would be too time-consuming and expensive for a prototype.
Because I chose to work with existing machines and software, I’ve had to make compromises. But I know that the technology works. So although the prototype doesn’t currently have the ideal composition, I know it will be possible to work with different materials in the future.
I am constantly thinking about how best to speak the language of the industry while at the same time innovating. I always try to show what’s achievable with the current resources we share, to inspire the industry that alternative prodution methods are possible.
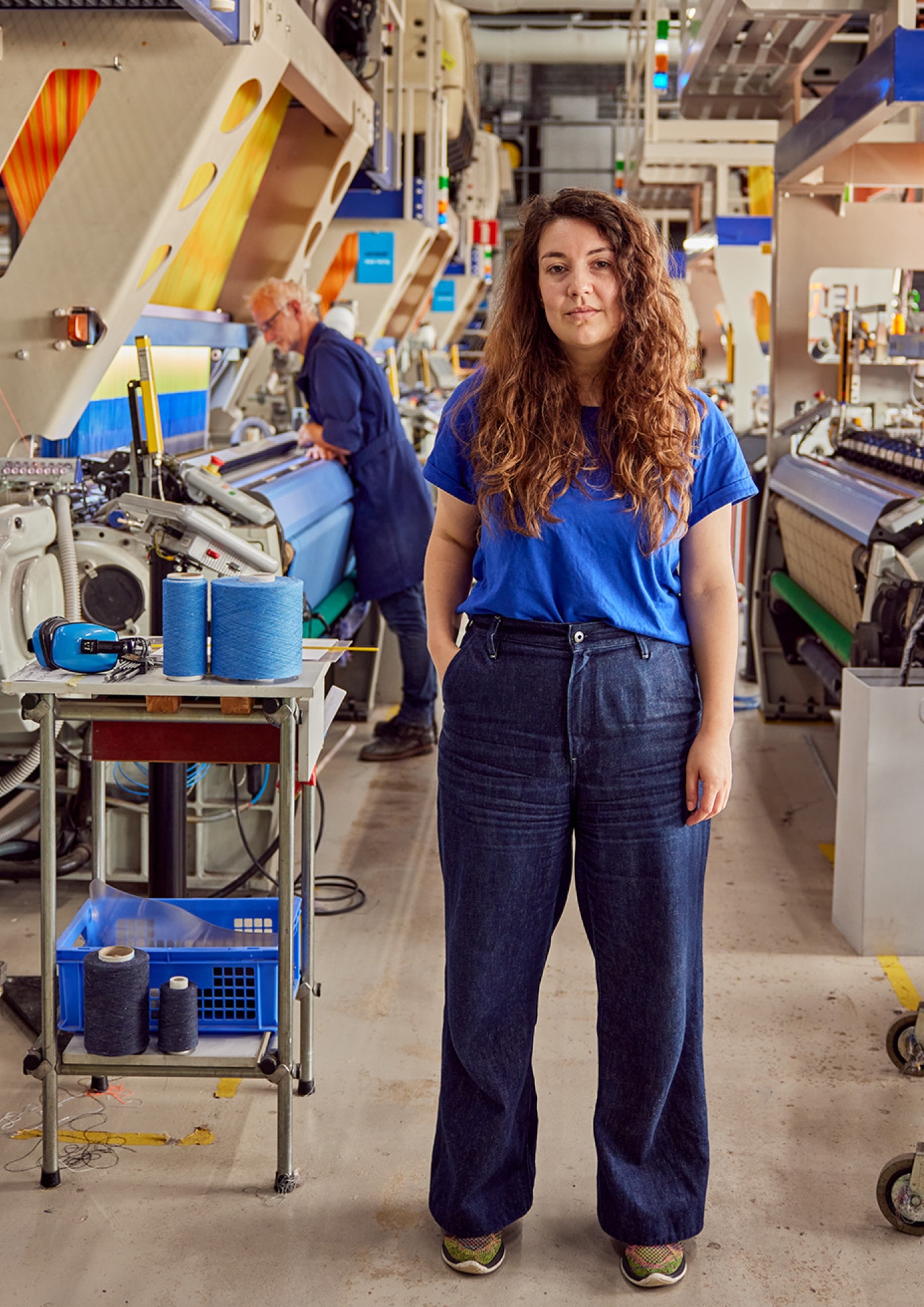
What vision of the future do you have regarding the 3D weaving technology you are developing?
With my work, my goal is to lay the foundation for a new approach to textile production. I hope that in the future we will think about textiles from the perspective of possibilities rather than relying on traditional methods.
By directly weaving a shape rather than a piece of fabric, we can better streamline the production process and minimise material waste. My technique automates the most labour-intensive part of garment production, reducing the labour needed and ultimately lowering costs. This makes it possible to manufacture closer to home, in the Netherlands or in Europe, reducing the environmental impact through decreased transportation emissions. In addition, by creating garments to size, we can respond much better to the wearer's desire and body, thus making clothes that fit better and therefore last longer, which can drastically reduce overproduction and waste.
Finally, what is the most important message you want to convey to our readers?
First of all, I hope that through my work, people will gain a greater appreciation for textiles. By showing the complex and beautiful technique of 3D weaving, I hope to open people's eyes to how textiles are actually made. I want to inspire both the industry and the new generation of young makers to actively contribute to improving the garment and textile industry.
Finally, I also want to inspire consumers to make different choices and start viewing clothing as more than a disposable product. By helping them understand that their clothes are created through a complex and intensive process, I hope consumers realise the substantial impact they can make.
More interviews
Suntex
Pauline van Dongen has developed a lightweight, solar-powered textile called SUNTEX.
Haptics of Cooking
Boey (Bo) Wang is dedicated to creating fully inclusive products for performing everyday tasks.
Meaningful Matter
Lotte Douwes transforms ceramic waste into new high-quality tableware and interior products. Her mission is to make the entire production process of porcelain and pottery circular. Because while the plate in your cupboard and that cup on your desk may seem ordinary, they are made from precious pieces of earth.
Omlab
Huub Looze and Margreet van Uffelen create items such as embankment tiles and birdhouses that help restore soil and biodiversity after use.
Resty
Designer Doreen Westphal and entrepreneur Ruud Zanders are turning vegetable waste from Dutch farmers into pure and healthy food. Operating under the name Resty, they process rejected mushroom stalks and misshapen tomatoes into delicious plant-based burgers and sausages.