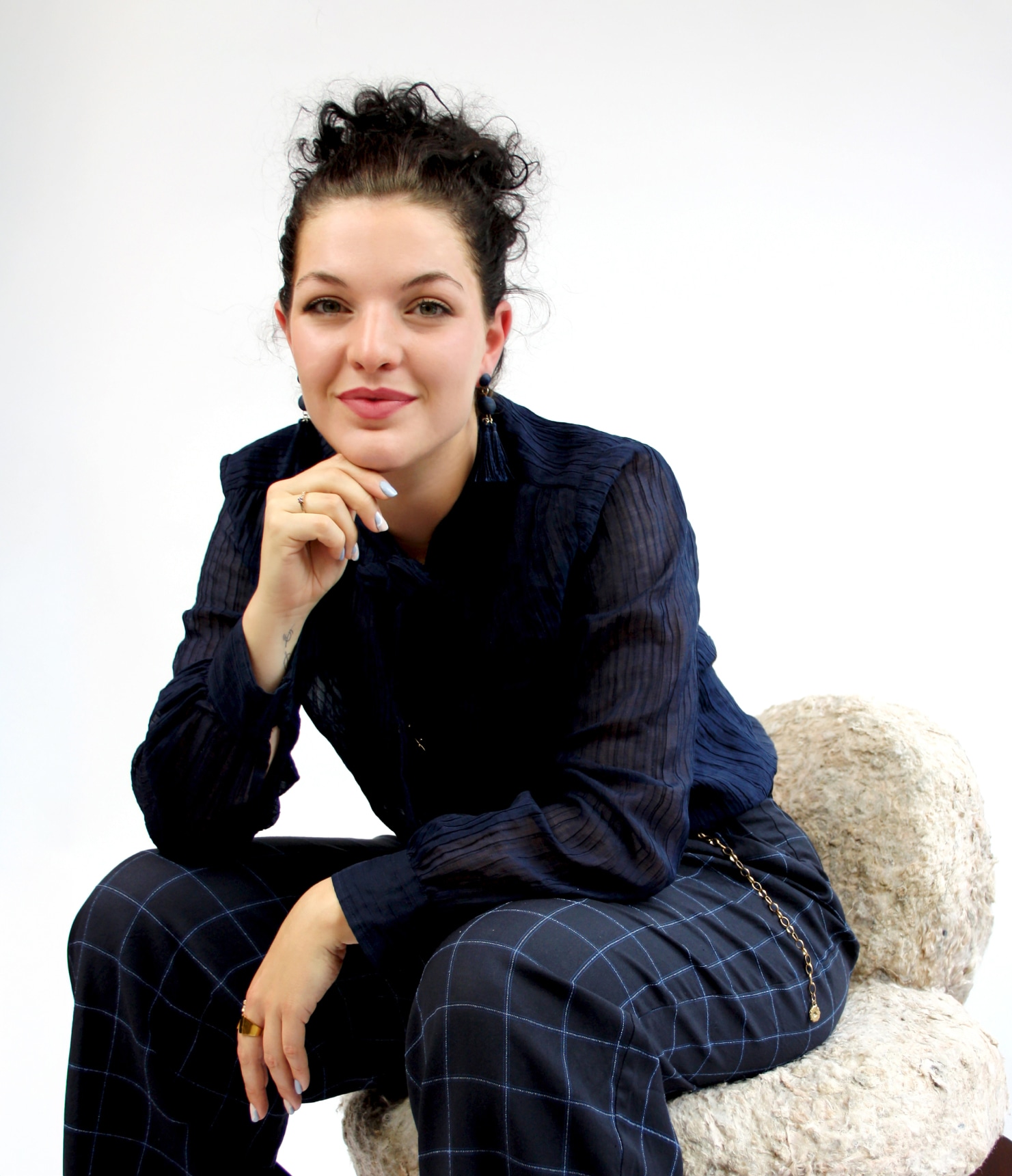
VivErdie Industries
Vivian Erdtsieck
Vifour is a textile made from recycled fabrics that can be recycled indefinitely. This circular material is used for interior products, such as acoustic wall panels, carpets, and furniture coverings. It's the first invention of Vivian Erdtsieck, whose company is researching renewable textile solutions.
And that is much needed, because massive quantities of textiles are discarded in the fashion industry. It's estimated that up to 80% of all clothing worldwide is either sent to landfills or incinerated, much of which is never sold or worn. Since many products combine various forms of textiles, this ‘waste’ can't usually be properly recycled.
We talk to Vivian three years after she participated in the first Secrid Talent Podium to discuss her solution to all that mixed textile waste, about connecting science and design, and her search for a business partner.
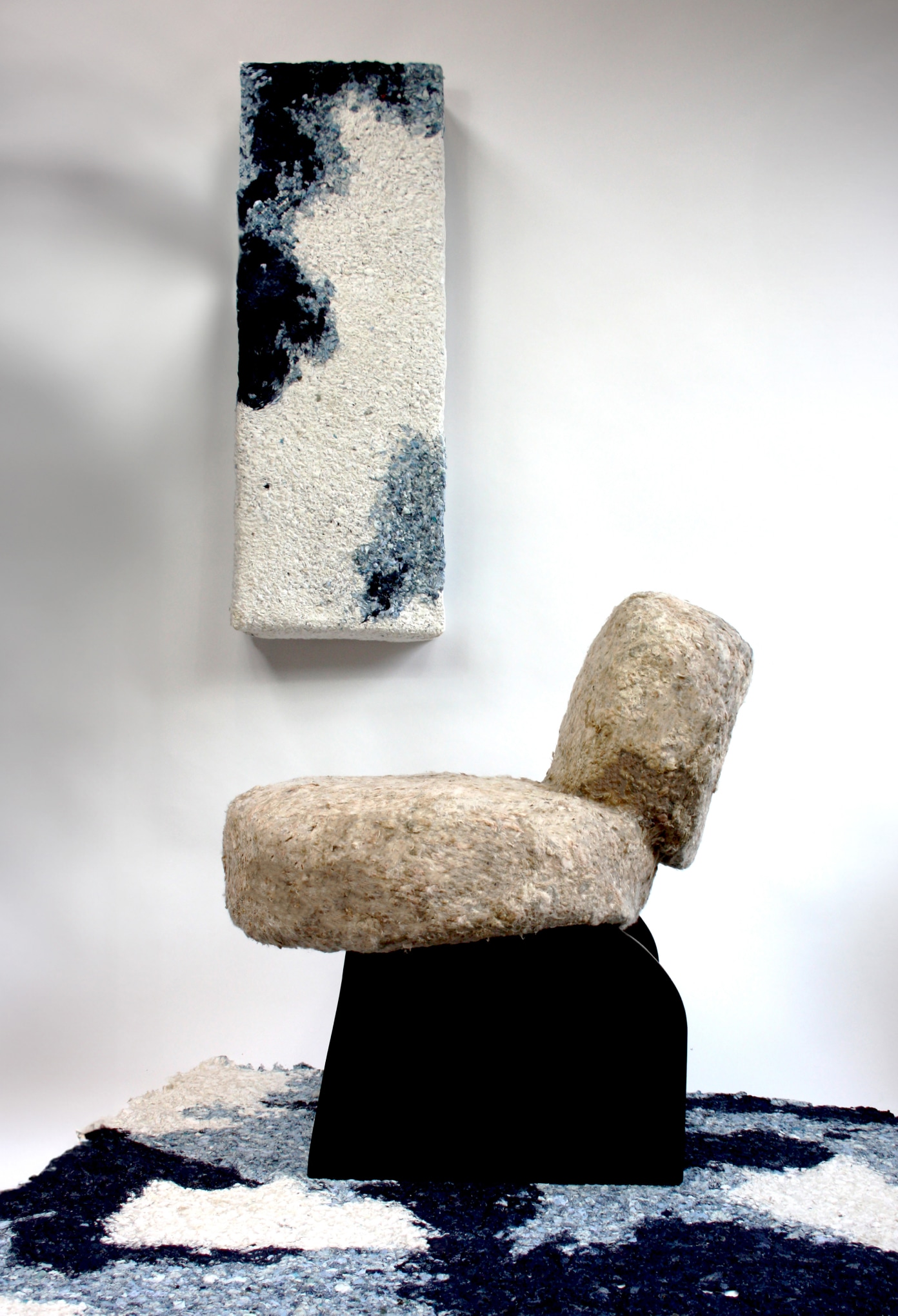
Photography: VivErdie Industries
Hi Vivian, it's been three years since you first took part in the Secrid Talent Podium with your closed-loop textile. How are you doing?
“Good! I'm in my studio in Driebergen working on some fabrics for my new collection. I want to present them at Material District in March. That's a match-making platform for innovative materials. So, I'm still making recycled and renewable textiles.”
What led you to start recycling textiles?
“I grew up in a creative and entrepreneurial family in Driebergen, a small village in the Netherlands. My mother made costumes, and I liked to help with that, so I became involved with fashion and textiles at an early age. After high school, I went to the fashion academy, but I soon discovered that I didn't quite fit in there.
Their main focus was on making new collections. I'm not opposed to that, but I kept wondering why we need so many collections—and especially so much fabric! To practice, we had to get swatches for each collection, but fabric stores would only sell you a minimum of half a meter of fabric. At one point, I had all those half meters in my closet, never to be used again. All that waste really bothered me.
Did you learn at fashion school how to make textiles from all those fabric scraps?
“No, that's why I went to the University of the Arts Utrecht (HKU), where I was able to experiment more freely with using all that textile waste. While on an exchange in Bratislava, I truly discovered my passion for textile making. We visited the places where raw materials like cotton are grown, and were given a full demonstration of the process, right through to the weaving of the textile.
Many fashion academies tell you how textiles are made, but they never actually teach you how to make them yourself. You never get much of a feel for its ecological impact or how much work goes into its creation.
For my graduation, I wanted to make a renewable collection, without using new textiles and producing waste. When I couldn't find the fabric I needed, I started making it myself.
So many unused textiles, that really bothered me.
Are large amounts of textile waste also a problem in wholesale fashion?
“Yes, what I experienced as a student also occurs on a large scale in the fashion industry. Globally, we generate an estimated 92 million tons of textile waste a year, much of which is never sold or worn. This waste could cover the whole of the Netherlands 11 times, or half of France. As much as 80% of all textile products worldwide end up in landfills or incinerators.
In my opinion, one of the biggest problems is that we want a new collection every year, and sometimes even more often than that. Fast fashion companies in particular choose to destroy many of their clothes. They produce a lot and offer that at extremely low prices, without including, for example, their ecological costs. Due to rapidly changing fashion trends, they put old collections on sale, causing materials to lose value even more quickly. Eventually, they throw them away to make room for new stock and to protect their brand value.
What also happens a lot these days is that people order three items of clothing online and return two. Many companies don't include the cost of processing those returns in their retail price. It's estimated that, as a result, about 30% of all returned clothing is incinerated unused. That amounts to 3.4 billion T-shirts! Getting rid of them and producing something new yields greater returns. That's crazy, don't you think? I want to put all this waste to good use.”
Why is so little of all that unused textile being recycled?
“We're often unaware that many of these cheap clothes use mixed materials, such as blends of polyester and cotton. The industry is already quite good at recycling monocultures, like pure wool or cotton. Blends, on the other hand, are difficult to separate and extremely expensive to recycle.
If a blended material is reused at all, it usually becomes weaker. As a result, recycling actually often means downcycling. It may still be repurposed as a lower-quality product in another industry, such as insulation material, but after multiple recycling processes it will eventually reach a point where it can no longer be recycled.”
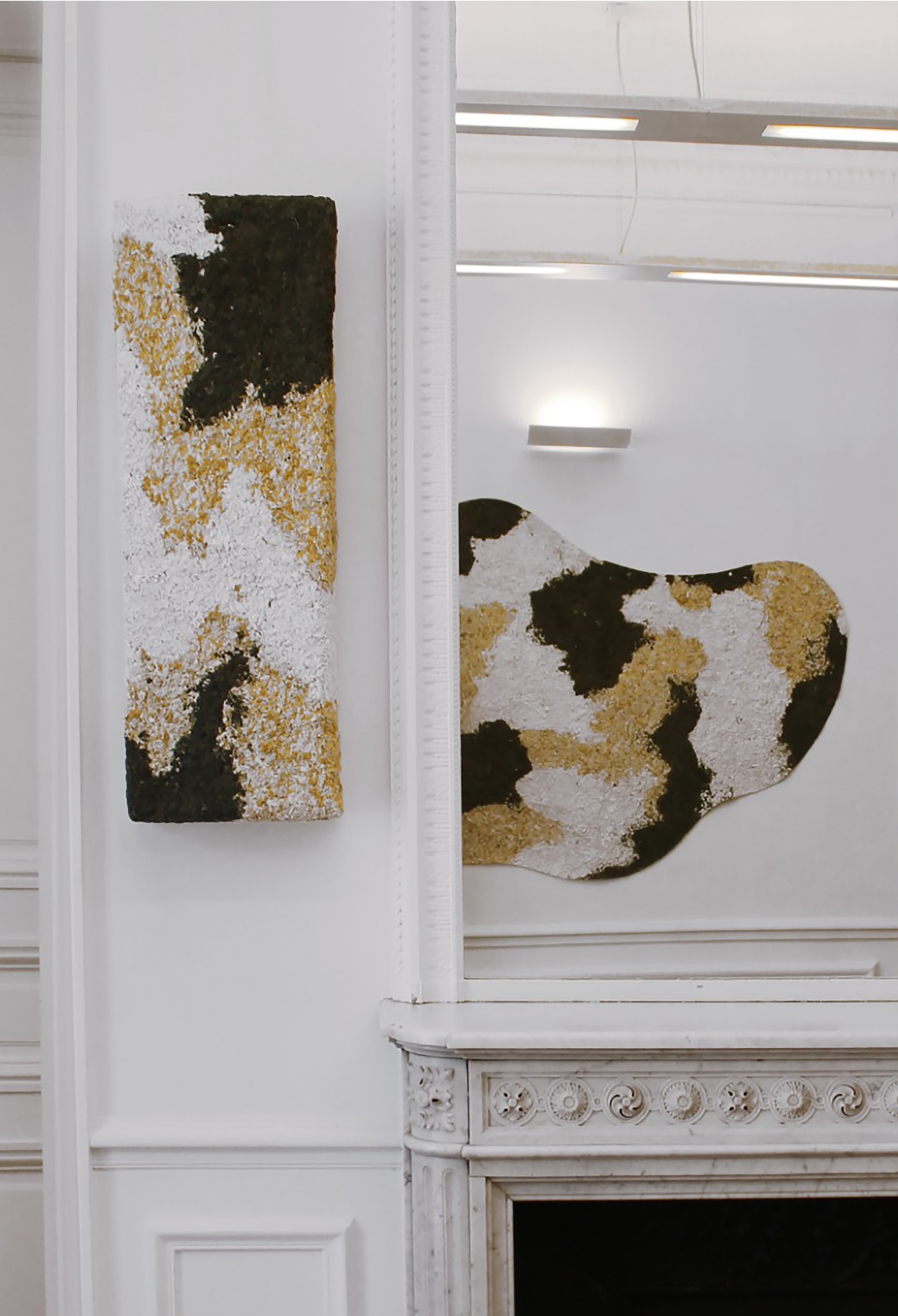
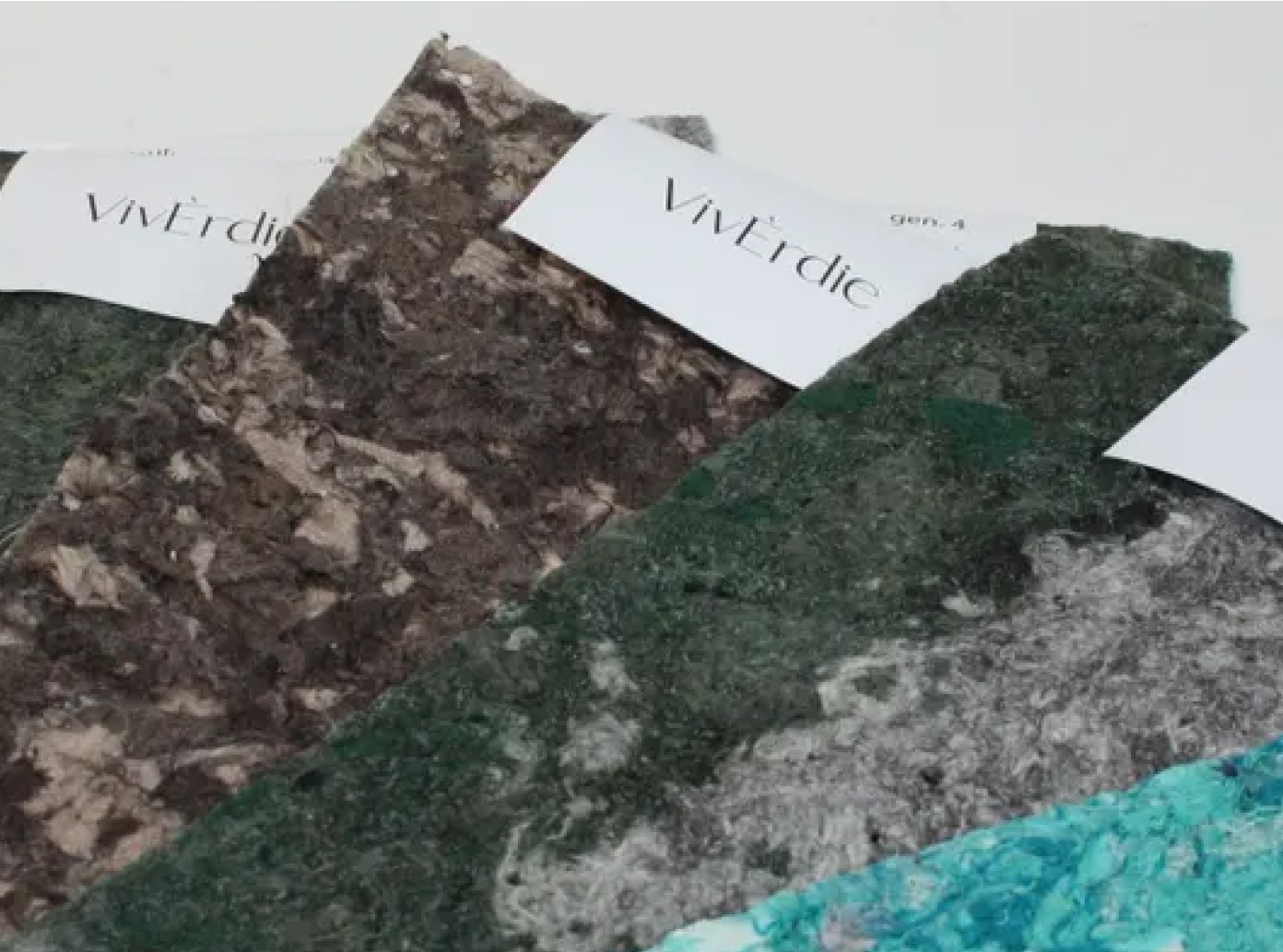
You specifically recycle that mixed textile waste. What's your solution?
“The textile I make is called Vifour. To make it, I specifically recycle those mixed textiles. I work with cutting waste from industry, used clothing or textiles, and sometimes return shipments. I first select everything I receive for color and then shred it, after which I roll it out and turn it into new textiles that can be used in interiors.
The magic of this material is a natural starch-based binder that I developed. This is a kind of glue that goes into the fibers of the shredded pieces and then hardens. Usually, the use of glue means a material has reached its end-of-life cycle, but after my binder dries up, the chemical process can be restarted. This means Vifour can always be broken down again into small pieces and reassembled, optionally with new pieces of fabric. This means you can repair it very easily and recycle it indefinitely.”
Is Vifour already being used to make interior products?
“Vifour is available as a textile in rolls, so designers can use it to make something with it. And I also make my own products with it. Sound-absorbing wall panels work quite well. I recently sold my first large order of these for an office building in Driebergen. I first create a frame with wood from Buurman, that is a construction site in Utrecht that sells second-hand building products. Then, I fill that frame with Dutch wool, which would otherwise be discarded.
I also make rugs, chairs, and sofas, but these are not yet being sold in large orders. I mainly make them to showcase Vifour's versatility. My company hasn't been around that long. In this way, I can show that a rug, for example, has lasted for three years unscathed.”
Can you tell us a little more about the quality of Vifour? For example, is it fireproof and water-resistant?
Yes, it's quite durable. It's UV-resistant and fireproof, which is especially important for wall panels. You can walk on it as a carpet and sit on it as a furniture covering. If it does break, you can iron a new piece of fabric onto it, or I can repair it quite easily, which means you don't have to buy a new product.
You can also drop a glass of water on it or clean it with a little bit of water or a vacuum cleaner. But it shouldn't be outside in the pouring rain. It's an interior product, after all.”
This means you can repair Vifour very easily and recycle it indefinitely.
Where do the fabrics you reuse come from?
“For my own collections, I use second-hand clothing. These come, for example, from the municipality. These are clothes that people drop off in clothing collection containers. Part of what doesn't sell ends up with me. I always pass mono-textiles like pure cotton on to someone else. I can recycle it, but because I can also process mixed textiles, I choose to focus on that.
I also buy clothes through the Refugee Foundation. They have second-hand stores throughout the Netherlands, and I work with the one here in Driebergen. A lot of the clothes they receive aren't sold and have to be picked up again for a fee. Before they're picked up, I go through them one last time to pick out some colors and pay them for that. For them, it's an extra source of income, and for me it's an unlimited resource.
I also work on commission. In such cases, I work mainly with deadstock fabrics and residual materials, such as commercial cutting waste. For example, I'm currently working with Kemkes, a Dutch clothing brand that works with second-hand fabrics. I use their cutting waste to make new textiles, which they then use to make their own bags.”
Can you create all the colors with the textiles you pick up?
“Yes. We have such an endless supply of textiles that it never takes me long to gather enough material for any color. Some colors are worn more, so I can find them faster. For very specific colors, the delivery time is sometimes a little longer. This is because I use the original colors of the textiles I collect, I don't dye them.
The color matching of my collection is about 80% compared to the swatches I make. There is always a bit of variation, and it's never completely even. I like that. Nature itself is dynamic. I like how this makes everything unique.”
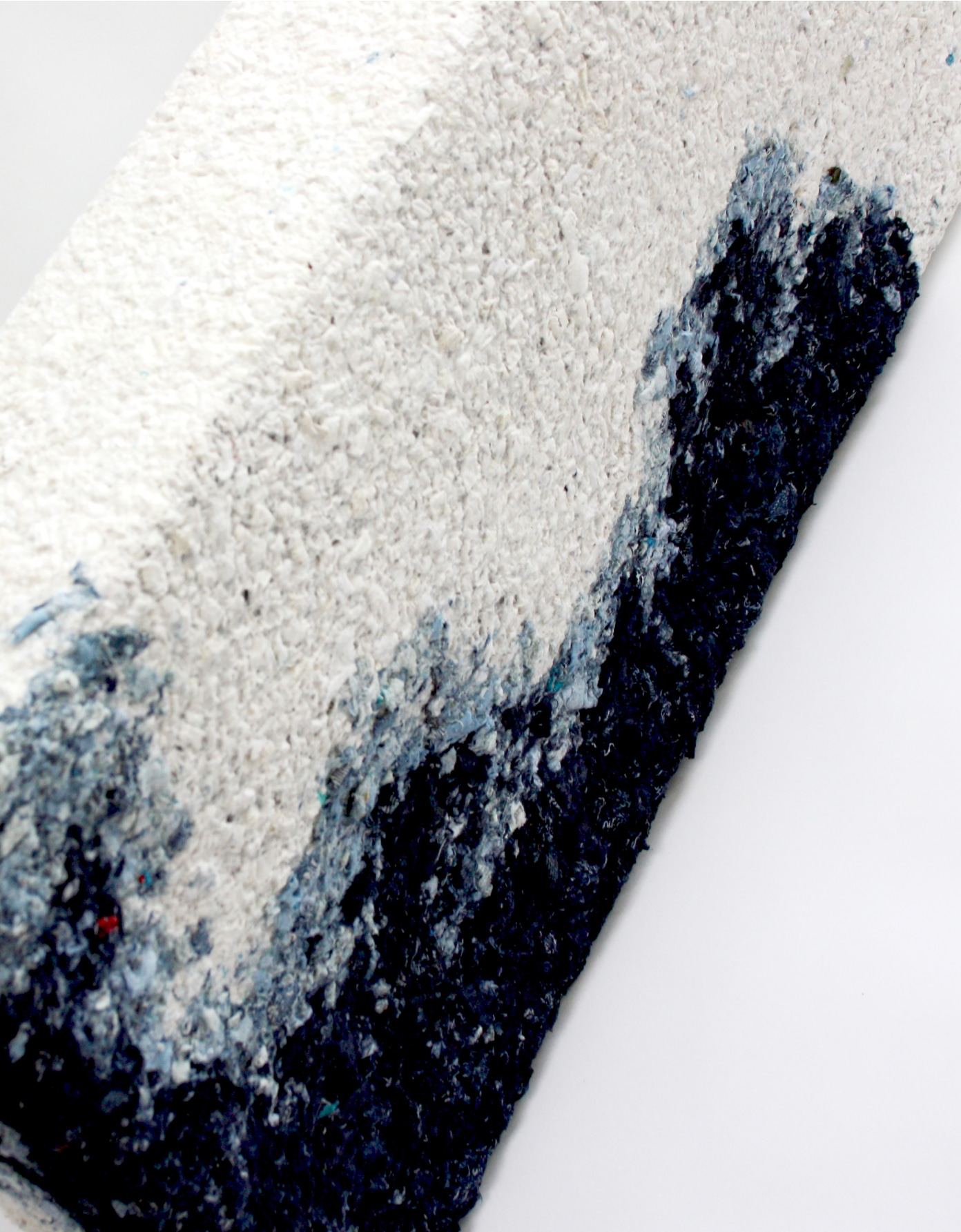

You now create your own color collections for your textiles. Why?
“Yes, I consciously make new color swatches. That's how I respond to consumer behavior, because we all like to have new things sometimes. However, no fabric is lost in the process, as it can always be reused. If you're tired of a product after five years, for example, you can return it and choose a new color. All you need to pay for is the manufacturing process. If you don't want a new item, I can use it to create something new myself.”
Your colors are dynamic, just like nature. As a designer, how do you see beauty?
“I really want to use my work to show the beauty of waste. We often think of waste as something dirty on the outskirts of society. I believe we should look at waste the same way nature does, as something that belongs. Everything can be reused.
And yes, I think aesthetics are incredibly important in this. A beautiful story is seen and read more. This is why I want to use my designs to translate textile waste into something beautiful that you want to have in your living room.
For me as a person and as a designer, if I am honest, this is less important. I just like to create functional products. I really enjoy it when textile waste becomes an acoustic wall panel that works really well.”
Besides being beautiful and functional, are your products affordable?
“We're pretty average in the market. For example, if you cover a wall with my wall panels, you spend less than on other quality sound insulation alternatives. Of course, you can buy insulation from the hardware store, which will be cheaper, but then you'll also have a poorer acoustic performance. The same goes for a rug, if you buy one from most fast-moving retail brands it is a lot cheaper, but my rugs are more affordable than most of the more durable options.”
You just sold your first big order. Are you already thinking about scaling up?
“Yes, I really want to scale up my production system. I'm already being asked to fill several walls with wall panels, and I need these kinds of assignments to grow. But in truth, my studio is too small to handle them efficiently. This is why I'm looking for a bigger space. I want to continue producing locally, but this can be anywhere in the Netherlands.
And I also want to switch from manual to machine production. I have the machine all figured out, but building it is expensive. I need investors for that. I'm currently creating an investment plan, and this summer I hope to start talking to people who want to help me with this.
A business partner would be nice in this process. Someone who can also help make my products more accessible. Now, I'm selling them through my website and I’m producing on demand, But if I can scale up, I can start working with an inventory and sell products through other companies or stores.”
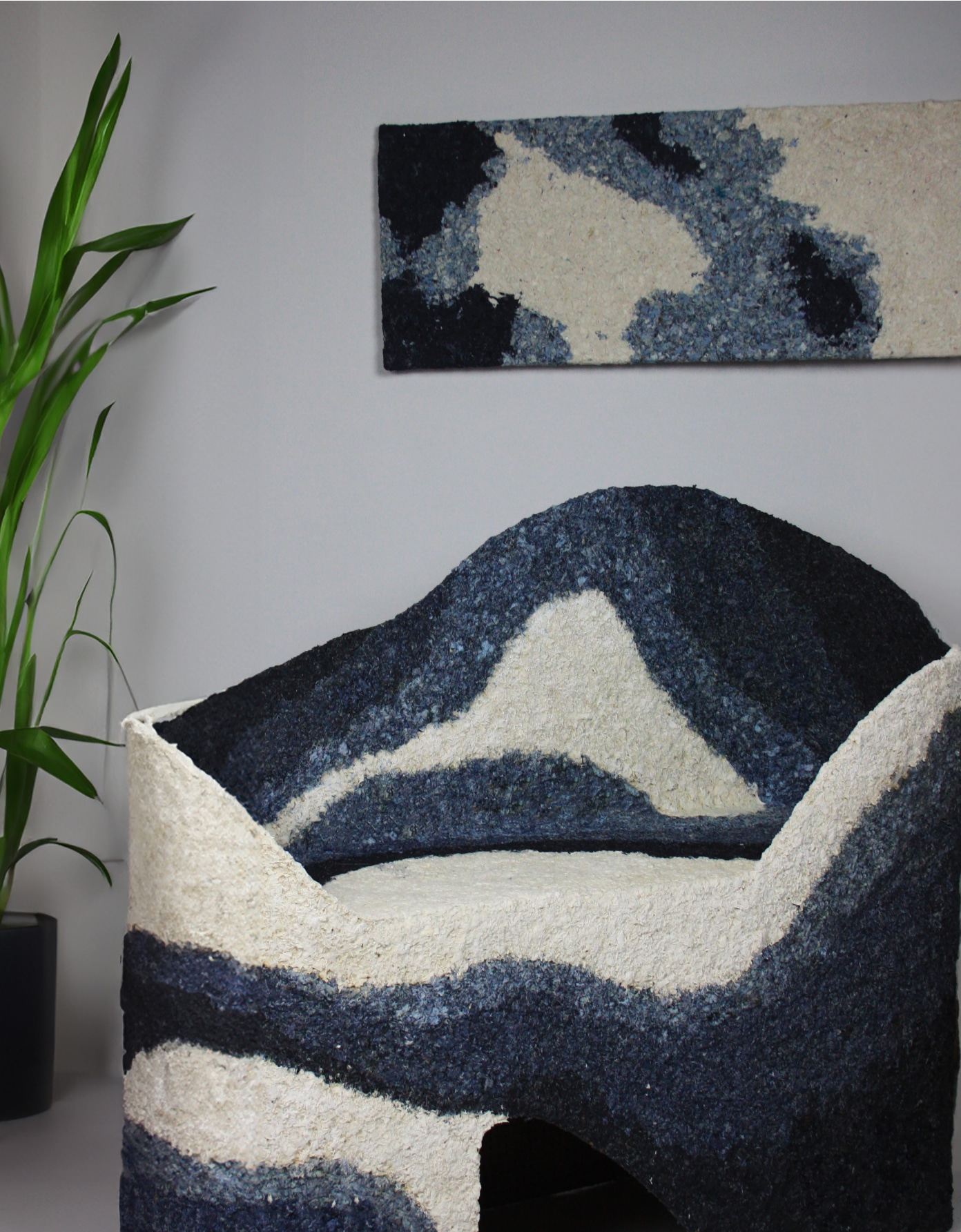
What are you looking for in a business partner?
“Ideally, I'd like to work with someone who understands business and marketing a bit better than I do. And someone with perseverance, a pioneer who is just as excited about this work as I am. You're taking on something pretty big together, which I find exciting. But I also have a strong need for that, so I would like to put out that call.
Advisers and sparring partners are good, but I already have those in my life. I have my father and my uncle, both of whom had their own business. My uncle even had a company that developed sustainable materials. In that respect, I'm incredibly lucky to have such a great support team. This is why I'm still doing well, despite being on my own.”
How do you look to the future? What will your company look like ten years from now?
“In ten years, I'll be doing even more material research within the circular vision I already have. At present, I have one material, which I want to market well first. But I also want to continue researching other renewable materials to develop more options.
As I envision it now, my company will bring together science and design. At the moment, these are often two distinct islands. I want to build bridges between them, I think I can play a role in connecting those two worlds. There's a company in England called Modern Synthesis that focuses on research, development, and textiles. They're a big source of inspiration for me.”
Summing up, what is the most important message you want to convey?
“I hope that people will become more aware of all the valuable raw materials that nature provides us with. Because then we will also see the value of what we throw away. Our waste should always be a valuable raw material itself – either for developing new products or for nature, so she can continue to give.”
More Interviews
Suntex
Pauline van Dongen has developed a lightweight, solar-powered textile called SUNTEX.
Haptics of Cooking
Boey (Bo) Wang is dedicated to creating fully inclusive products for performing everyday tasks.
Meaningful Matter
Lotte Douwes transforms ceramic waste into new high-quality tableware and interior products. Her mission is to make the entire production process of porcelain and pottery circular. Because while the plate in your cupboard and that cup on your desk may seem ordinary, they are made from precious pieces of earth.
Studio Milou Voorwinden
Milou Voorwinden is innovating the existing fashion and textile industry by developing 3D weaving techniques.
Omlab
Huub Looze and Margreet van Uffelen create items such as embankment tiles and birdhouses that help restore soil and biodiversity after use.
ForestGuard
ForestGuard is an advanced wildfire prevention system. This device detects forest fires within the first 15 minutes and helps communities worldwide to protect their valuable forests and natural resources. An integrated monitoring system can help to manage a fire before it starts or turns into a full-blown fire.